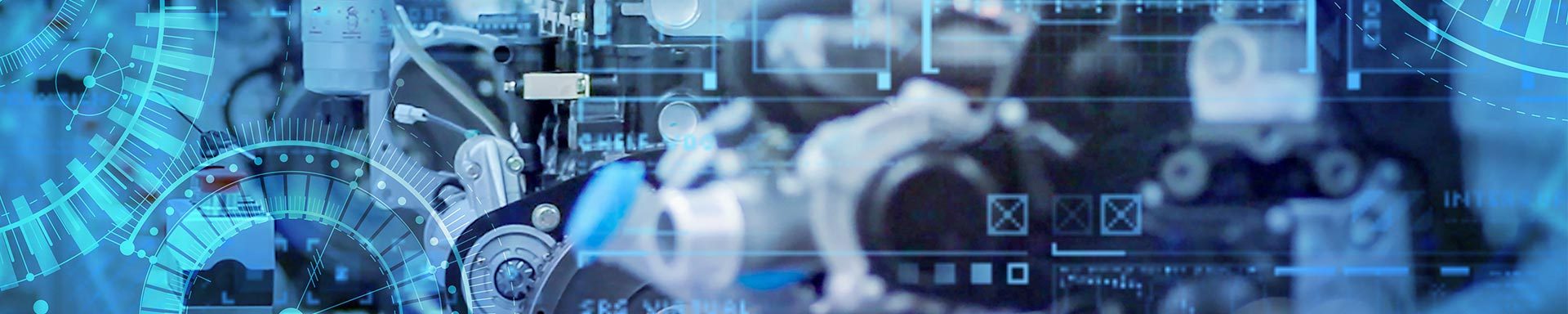
Application and Precautions of Centrifugal Pumps in Wire and Cable Production
2025-07-17 14:04Centrifugal pumps are widely used in wire and cable manufacturing for cooling water circulation, lubrication systems, and wastewater treatment due to their simple structure, stable flow, and easy maintenance. Below are their key applications and important considerations.
I. Main Applications of Centrifugal Pumps
1. Cooling Water Circulation System
Purpose: Cooling wire drawing machines, stranding machines, and extruders to prevent overheating.
Features:High flow rate, low head, suitable for open or closed-loop cooling systems.Typically equipped with filters to prevent clogging.
2. Lubrication System (Oil/Water Cooling)
Purpose: Delivering low-viscosity lubricants or emulsions for wire drawing dies and conductor surface lubrication.
Features:Requires oil-resistant materials (e.g., stainless steel or coated cast iron).
3. Wastewater Recycling and Treatment
Purpose: Discharging or recycling cooling wastewater and cleaning solutions.
Features:If wastewater contains solids, use wear-resistant centrifugal pumps or install strainers.
II. Key Considerations for Pump Selection
Flow Rate & Head:
Cooling systems must account for thermal load (typical flow: 10-50 m³/h).
Lubrication systems require stable low-pressure delivery (head: 10-30 m).
Media Compatibility:
Clean water/coolant: Standard cast iron or stainless steel pumps.
Oily/chemical media: Corrosion-resistant materials (e.g., 304/316 stainless steel).
Wastewater with solids: Use open impellers or install filters.
Temperature Resistance:
Standard cooling water (≤80°C): General-purpose centrifugal pumps.
High-temperature fluids (e.g., extruder cooling): High-temperature seals (e.g., graphite mechanical seals).
Leakage Prevention:
For oils or chemicals, use mechanical seals or magnetic drive centrifugal pumps (leak-free).
III. Operational Precautions
1. Pre-Start Checks
Ensure the pump is primed (no air inside) to avoid cavitation damage.
Verify correct motor rotation (reverse rotation reduces flow).
2. Operation & Maintenance
Avoid dry running: Operating without liquid damages mechanical seals.
Regular cleaning: Coolant impurities can clog impellers—clean strainers periodically.
Monitor vibration/noise: Abnormal sounds may indicate bearing wear or impeller imbalance.
3. Long-Term Storage
Drain liquid to prevent scaling/corrosion.
Lubricate mechanical seals to prevent aging.
IV.Industry Application Examples
Copper rod continuous casting/rolling cooling: Multiple centrifugal pumps in parallel for high-flow cooling.
Cable sheath extrusion cooling: High-temperature centrifugal pumps + plate heat exchangers for precise temperature control.
Wire drawing oil circulation: Stainless steel centrifugal pumps + magnetic filters for extended lifespan.
Note: For special media (e.g., strong acids, high viscosity), consider corrosion-resistant centrifugal pumps or switch to screw/gear pumps.
Proper selection and maintenance significantly enhance the efficiency and longevity of centrifugal pumps in wire and cable production!